CAPABILITIES
Swiss Machining/ Swiss Turning Service
Get highly precise and small parts with Prolea’s Swiss turning services. Our automated 3 and 5-axis Swiss CNC machines produce complex and high-length-to-diameter parts for diverse industries.
- Lead time as low as 1 day
- Tolerance down to ± 0.0004″
- Small parts as low as ⌀ 0.3mm
- ISO 9001:2015 certified
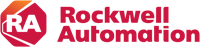
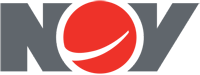
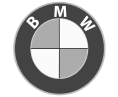
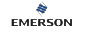
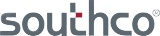
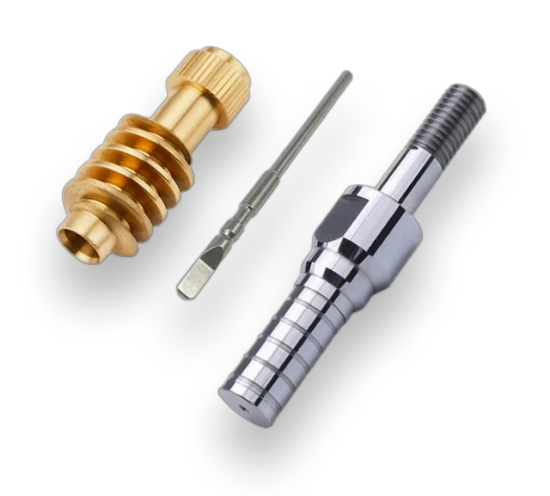
All uploads are secure and confidential.
Our Swiss Turning Service
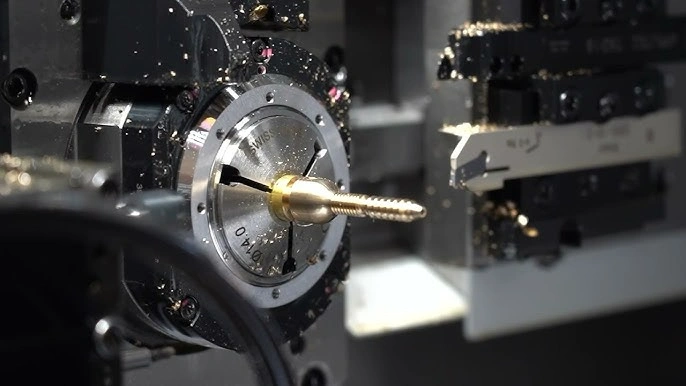
Swiss-style lathe features a movable headstock where the work bar gets attached for the turning in a collet or chuck, depending upon the size. If the bar is very tiny, the collet can attach it with a great degree of stability with the help of guide bushing. As a result, the bar stock is not exposed directly to the lathe bed and turning tooling, allowing the material to be turned quickly and securely inside the machine without deflection.
Swiss-turned Components: Swiss-turning components are extremely accurate and conform to the strictest tolerances. The Swiss turning machining is capable of high-volume production.
Our Swiss turn machining facility has multi-axis advanced machinery and experts working on creating small and miniature parts across all industries. You get unlimited material options, finishes, and custom tooling. We offer the highest precision and competitive prices for all volumes, from small batches of prototypes to full production runs.
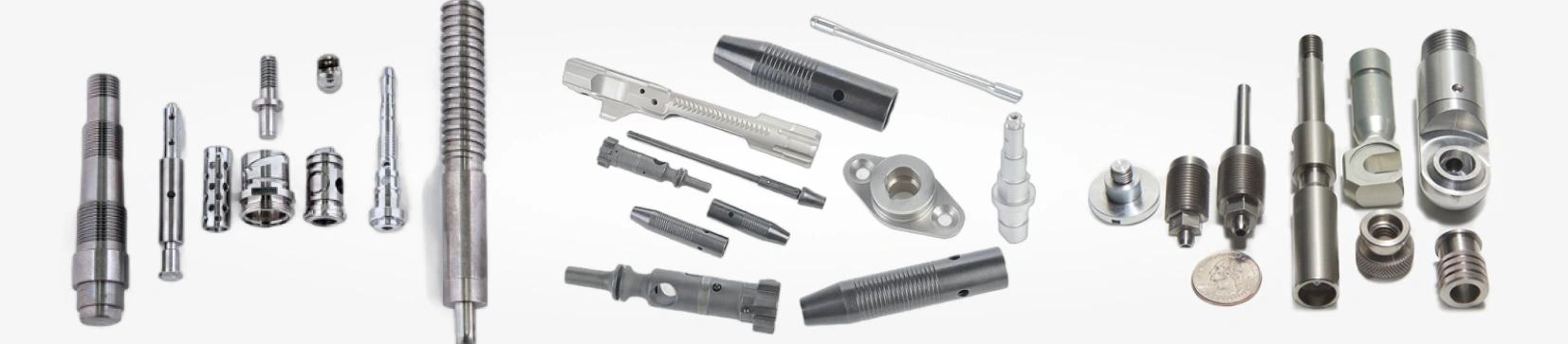
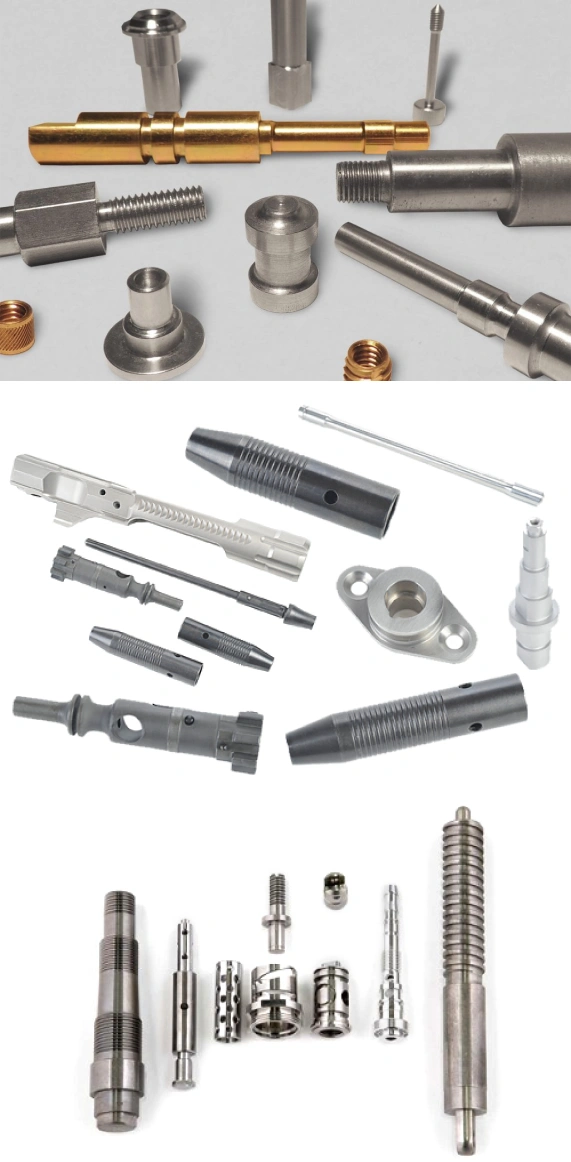
Prolean’s Machining Services
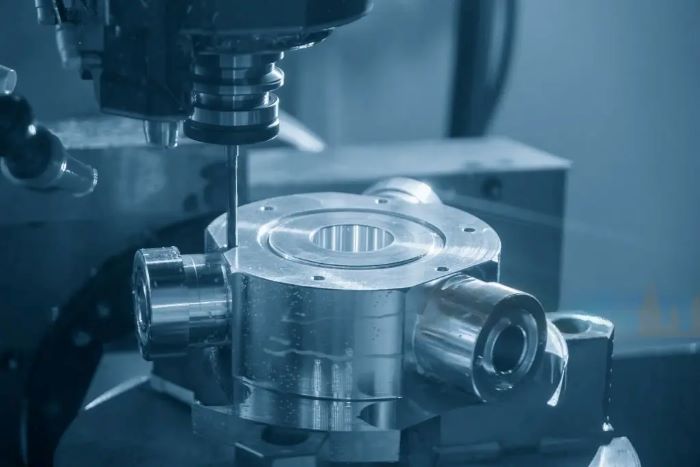
CNC Milling
Our CNC milling services use 3, 4, and 5-axis machines for complex parts and fine details. Live tooling allows for versatile, detailed features like engine blocks, gear profiles, and medical implants.
Suggest Industry Application:
Multiple Industries
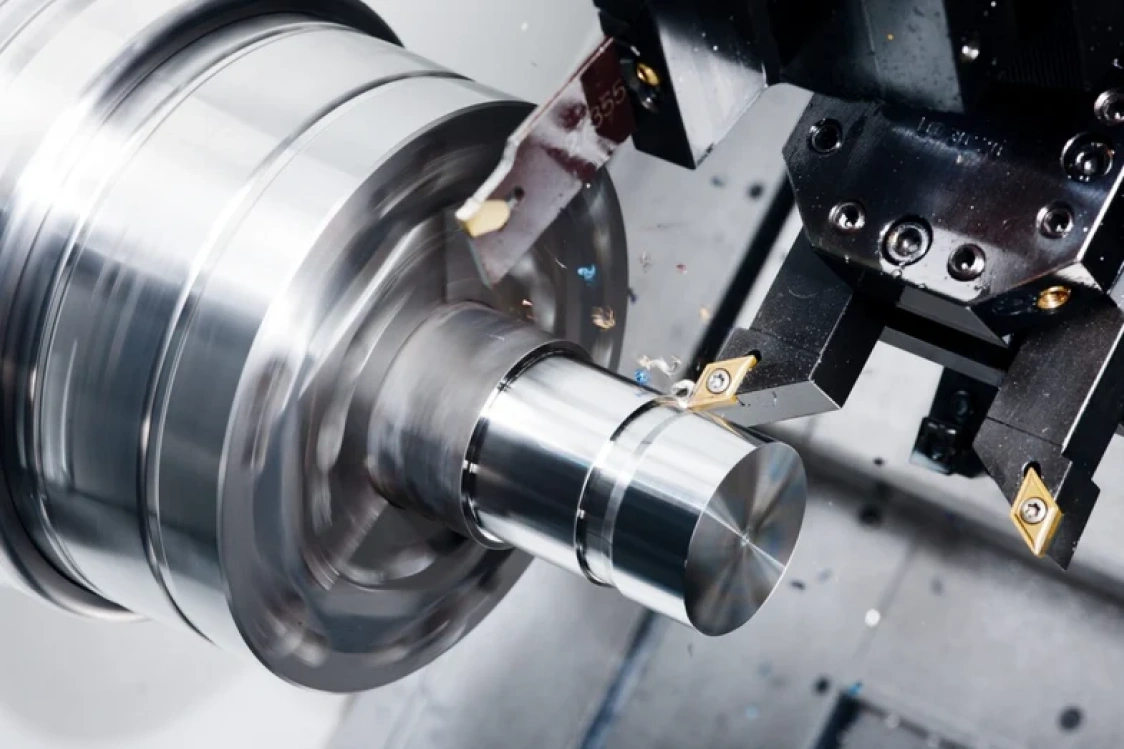
CNC Turning
CNC turning rotates workpieces while cutting tools remove material. It’s used for cylindrical shapes like shafts and pins, and is quick and flexible for prototypes and end-use parts.
Suggest Industry Application:
Multiple Industries

CNC Turn Milling
The CNC turning milling service combines turning and milling operations into a single-machine setup, allowing for the creation of intricate geometries on a single workpiece.
Suggest Industry Application:
Multiple Industries
Our Swiss Turning Capabilities
Capabilities | Description |
As Machined Finish (Ra) | 8 μm |
General Tolerance | ± 0.0004 in (0.0102 mm) |
Critical or Precision Tolerances | ± 0.0001 in (0.0025 mm) |
Maximum Outer Diameter | 1.25 in (32 mm) |
Maximum Length-to-Dia. Ratio | 4:1 |
Material Capability | Metal and plastics |
Inspection and Quality Control | Laser & ultrasonic inspections, CMM machine measurements |
You Have a Great ,We are Here to Help !
Try Prolean Now!
How to Order Parts?
Get a free quote from a real engineer; once we receive your design, our engineer will review it and send you a quote as fast as one hour.
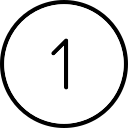
Get A Quote Immediately
Upload your design or email our engineer directly and get your quotes as fast as one hour.
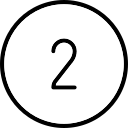
Start Production
Your parts will be made once your orders are confirmed. Besides, you will get real-time order updates of the production status from our order tracking system.
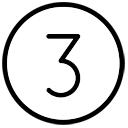
Receive Your Part
After all parts pass QC inspection, they will be well packed from transportation accidents. Then, your custom parts are delivered straight to your doorstep.
How Does Swiss Turning Work?
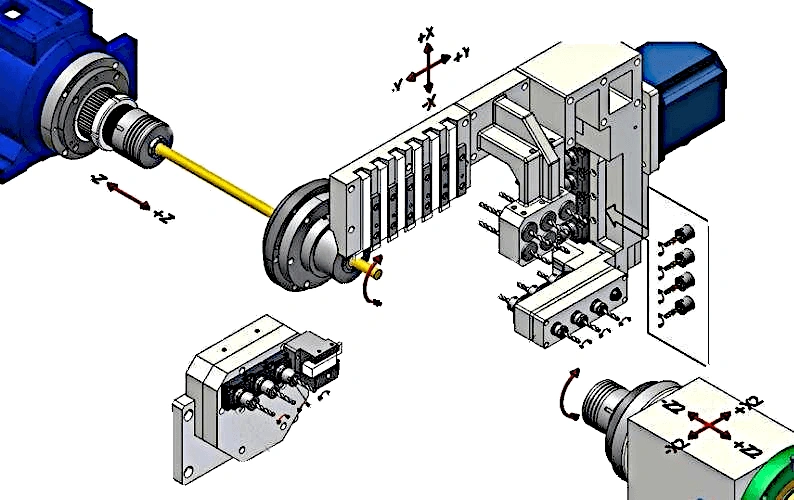
A Swiss-type lathe uses rotating cutting tools that feed the workpiece through a guide bushing. All the process variables and tool movements are computer-controlled. This setup ensures high precision for small and complex components.
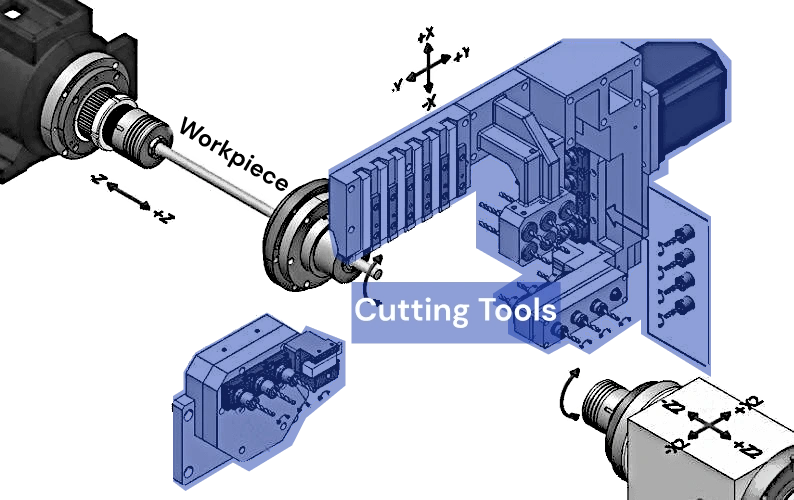
Tool Setup
The precise alignment of cutting tools along the rotating workpiece within the Swiss-type lathe. It can accommodate multiple tools on a tool post or turret, enabling various operations like milling, drilling, or turning.
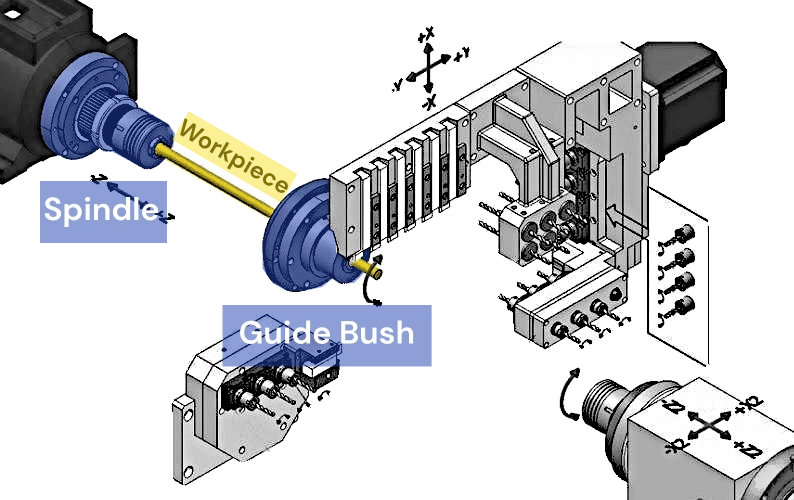
Material Feed
The workpiece is fed through a guide bushing, which provides support and maintains rigidity throughout the process. The guided feeding stabilizes the workpiece and minimizes the tool defection.
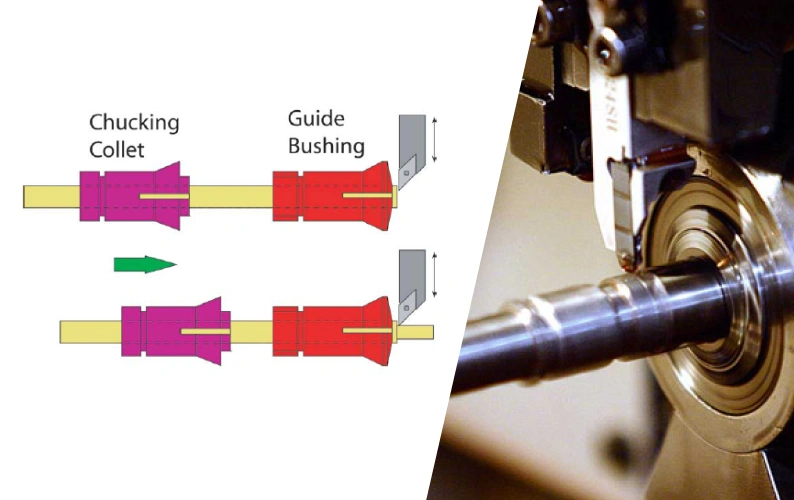
Swiss Turning
As the workpiece rotates and moves axially, the tools remove the material informs of small chips. The synchronized movement of the workpiece and the cutting tools creates intricate features with high accuracy.
Swiss Turning Material Options
Practically any material that can be machined using a standard CNC lathe or mill can be Swiss machined. Some examples of materials that can be used are listed below:
Metal
Aluminum Alloys
Aluminum Alloys
Aluminum alloys are known for being lightweight, having corrosion resistance, excellent thermal conductivity, and strengths (vary on alloying elements). They are highly machinable and offer high production speed.
- Grades: 2007, 2017A, 5083, 6060, 6061, 6082, 7075, etc.
- Applications: Aerospace components, automotive parts, sheet metal products, structural parts.
Stainless Steel Grades
Stainless Steel Grades
Stainless steel is one of the most common metals used in CNC machining. Steel alloys provide corrosion resistance, high mechanical strength, ductility, and excellent machinability.
- Grades: 303, 304, 316L, 316Ti, 304L, etc.
- Applications: High-strength and durable parts for automotive, food processing, medical equipment, etc.
Steel Grades
Steel Grades
Steel grades provide high tensile strength, good plasticity, and varying hardness & ductility. The machinability also varies on particular alloy grades. Steel CNC machining produces durable, wear-resistant, high-strength, and heat-treatable parts.
- Grades: S235JR, C45, C40, S355J2G3, 90MnCrV8, 16MnCr5, 25CrMo4, 42CrMo4, etc.
- Applications: Automotive parts, machinery components, structural applications, tool and die manufacturing.
Brass Grades
Brass Grades
Brass is a copper alloy that offers good conductivity, formability, strength, and corrosion resistance. Brass grades are also easy to machine and the machined parts can be solder and braze. easily.
- Grades: Ms58 / CuZn39Pb3
- Applications: Electrical and thermal components, decorative items, etc.
Titanium Grades
Titanium Grades
Titanium grades are renowned for exceptional strength-to-weight ratio, corrosion protection, and biocompatibility. The machining of titanium is used for lightweight and durable parts that can withstand harsh environments.
- Grades: Grade 2 / Grade 5 (Ti-6Al-4V)
- Applications: Aircraft structural parts, medical implants, oils and gas structures, and high-stress components.
Plastic
ABS
ABS
ABS is popular in machining due to its high tensile strength and toughness. It can create parts with excellent impact-resistant, wear-resistant, flame retardantdency, and also leaves good as a machined finish. It is often used as a metal replacement in some automotive and marine applications.
Acrylic (PMMA)
Acrylic (PMMA)
Acrylic or PMMA is a transparent and tough thermoplastic with excellent surface hardness, weather resistance, wear and abrasion resistance, and chemical inertness. The machining of acrylic surfaces can weaken the transparency, but further surface polishing can achieve that. Acrylic is ideal for applications requiring optical transparency or as a cost-effective alternative to polycarbonate.
Polycarbonate (PC)
Polycarbonate (PC)
Polycarbonate is also a transparent plastic but is more durable and shatterproof, than acrylic. It is a UV-stabilized and flame-retardant material. While machining, the PC is prone to stress cracking and requires slow feed rates and sharp tools The use of Polycarbonate machining is widespread, in food and beverage, packaging, medical devices, eyewear, electronics, etc.
PEEK
PEEK
It is high-performance CNC plastic with excellent mechanical strength, fatigue resistance, chemical resistance, and thermal stability. But it can be more expensive than other plastic materials. Some application examples include tubes, bearings, seals, valves, and medical implants.
Polypropylene (PP)
Polypropylene (PP)
Polypropylene is a CNC plastic material used in applications requiring high elongation and low flexural modulus. It has a transparent black-and-white appearance. Machining PP is mainly used for prototypes and large-size products like storage items.
Swiss Turned Parts Finishes
The swiss turned parts can be finished using different techniques to achieve specific surface properties and appearance. At ProleanTech, we have various surface finishing options for metal milling and plastic milling parts, tailored to your needs.
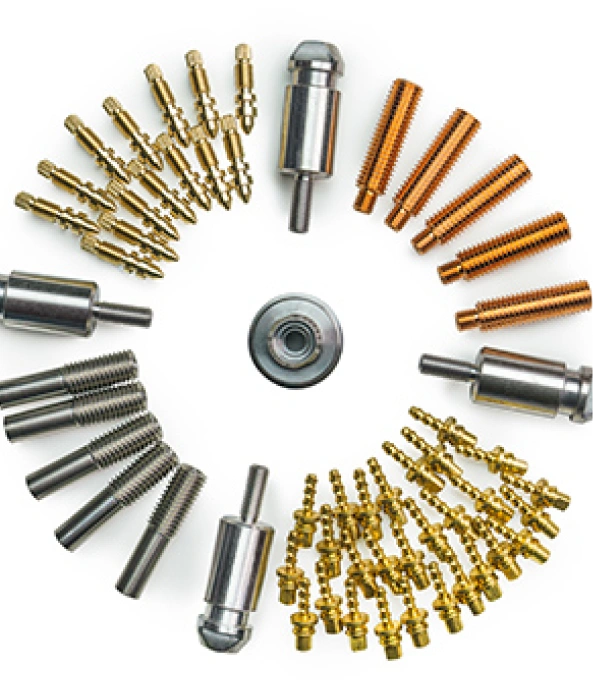
As Machined:
This finish refers to parts just after the machining process, sometimes followed by minor grinding. It contains tool marks, small burrs & chips, but provides tight tolerances. This finish is suitable when aesthetics is not a requirement.
Bead Blast:
Bead blasting strikes the tiny glass, ceramic, or other beads on the machined surface at high pressure to remove tool marks, burrs, chips, and other surface irregularities. It produces a light and smoothie texture with an attractive appearance.
Anodized:
The CNC-machined aluminum or non-ferrous parts can be anodized, which refers to adding and protective oxide layer on their surface. Anodized surfaces resist harsh environments and save the parts from corrosion, wear, and surface degradation.
Polishing:
Polishing can be applied through electrochemical and mechanical methods. It produces a smooth and fine, mirror-like finish with Ra as low as 0.3 μm. This surface finish is preferred for machined parts if low-surface friction is essential for performance or aesthetics is important.
Try Prolean Now!
Swiss Turning vs Conventional Turning
Swiss lathe offers distinct advantages over Conventional Turning, making it an ideal choice for intricate and precision machining. Discover the key features that set Swiss Turning apart:
Swiss Turning
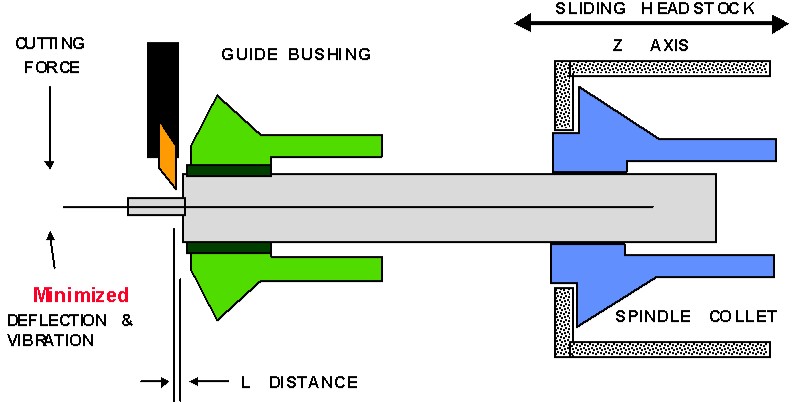
Conventional Turning
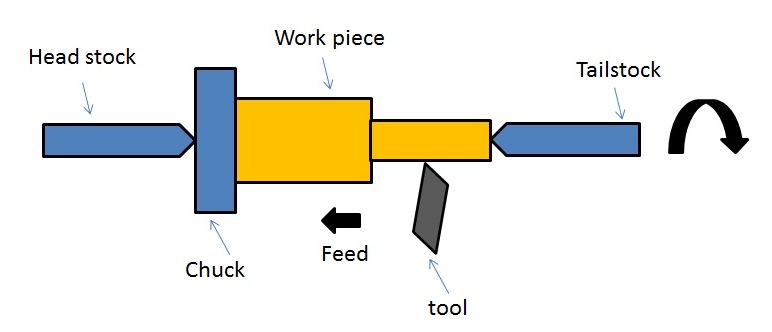
- Advanced Headstock Design: Swiss lathes feature a moving headstock, allowing precise repositioning along the z-axis during the machining process.
- Segmented Machining Process: Swiss machining ensures high consistency and accuracy, ideal for CNC-turned parts with stringent tolerances.
- Superior Guide Bushing Support: swiss style lathe reduces deflection and allows deeper cuts in a single pass, perfect for machining slender parts.
- Enhanced Cycle Times: Swiss style lathe offer multi-axis capabilities (ranging from 7 to 13 axes) significantly reduce manufacturing times for complex geometries.
- Oil-based Coolant System: Swiss turn offers better lubrication, reduces friction and heat generation, enhancing tool life and part quality.
- Reduced Post-Processing: Produces fine and precise parts, often eliminating the need for secondary finishing processes.
- Cost-Effectiveness for Large Runs: Ideal for high-volume production of complex parts, offering long-term economic benefits despite the higher initial cost.
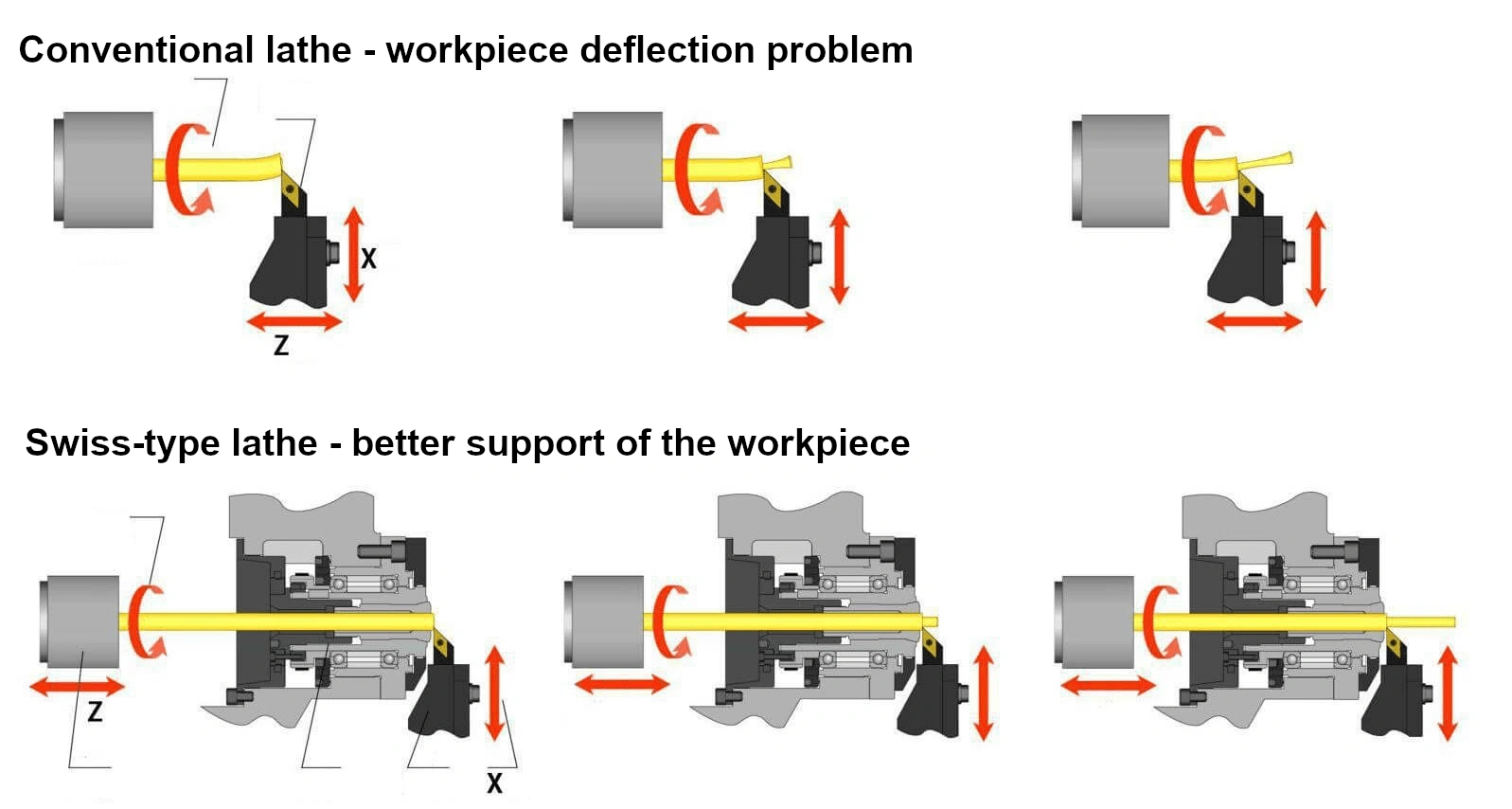
Swiss Turning offers better support of the workpiece compared to Conventional Turning because it uses a guide bushing that holds the workpiece close to the cutting tool. This setup minimizes deflection and vibration, leading to higher precision, smoother finishes, and improved overall quality, especially for long or slender parts.
Benefit of Using Swiss Turning
Swiss turning service employs swiss-type lathes for efficiently producing small, intricate parts. This technique is characterized by several significant benefits:
- High Precision: Enhanced precision due to reduced deflection.
- Part Consistency: Delivers uniform quality across large batches.
- Complex Part Production: Equipped for manufacturing complex parts with its multi-axis and tool capabilities.
- Synchronous Operations: Increases efficiency with simultaneous operations.
- Less Secondary Processing: Reduces the necessity for additional post-machining processes.
- Improved Surface Finish: Achieves better finishes at higher operational speeds.
- Automation: Features like automatic bar feeders and CAM programming minimize the need for manual intervention.
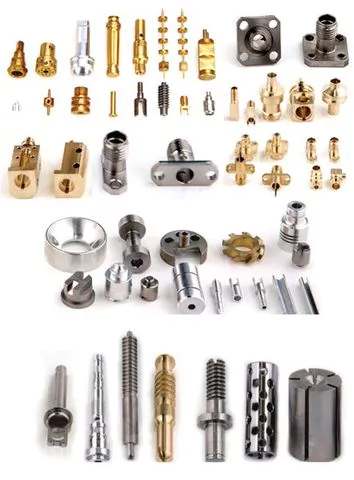
Try Prolean Now!
3 Ways to Ensure Perfection
Standards
GENERAL TOLERANCE
For metals, the standard is ISO-2768 fH (fine)
For plastics, the standard is ISO-2768 mK (medium)
Metric threads tolerances:ISO 965-1 standard UN Threads Tolerances: ASME B1.1-2003 standard
knurling: ISO13444:2012 standard Our factory is ISO 9001:2015 certificated
Visual inspection and Protection
Constant visual inspection conditions
Quantification of cosmetic surface quality
Process requirements
Part cleaning and Protection
Quality Inspection Report
Inspection Confirmation
Dimensional confirmation
Appearance confirmation
Quality documentation
Try Prolean Now!
Swiss Turning Applications
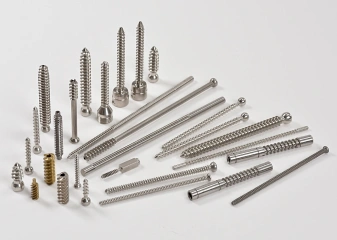
Medical Devices
Surgical instruments, bone screws, dental implants, and components for orthopedic devices, where high precision and smooth finishes are crucial.
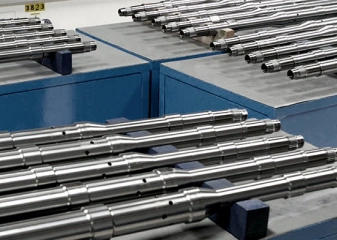
Aerospace
Small, high-precision parts such as shafts, connectors, and fasteners that require tight tolerances and consistent quality.
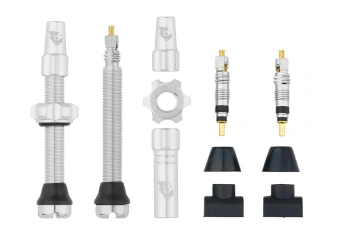
Automotive
Precision components like fuel injector nozzles, valve stems, and sensor components that require fine detail and reliable performance.
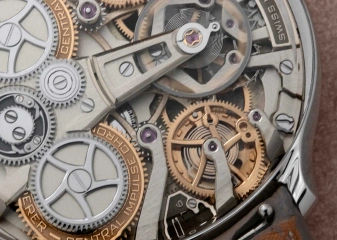
Watchmaking
Small gears, shafts, and other intricate components in watches, where precision and smooth operation are essential.
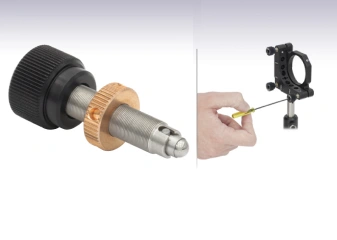
Optical Industry
Precision components used in optical instruments, such as lenses and small adjustment screws, which require high accuracy.
Swiss Turned Parts Gallery
Swiss Turning FAQs
Is Swiss CNC machining more expensive than regular CNC?
How does a Swiss CNC machine work?
What is the primary difference between Swiss Turning and CNC Turning?
How does the part complexity influence the choice between Swiss and CNC Turning?
How do CNC Turning services adapt to high-volume production needs?
Get Your Parts Made Today
All uploads are secure and confidential.